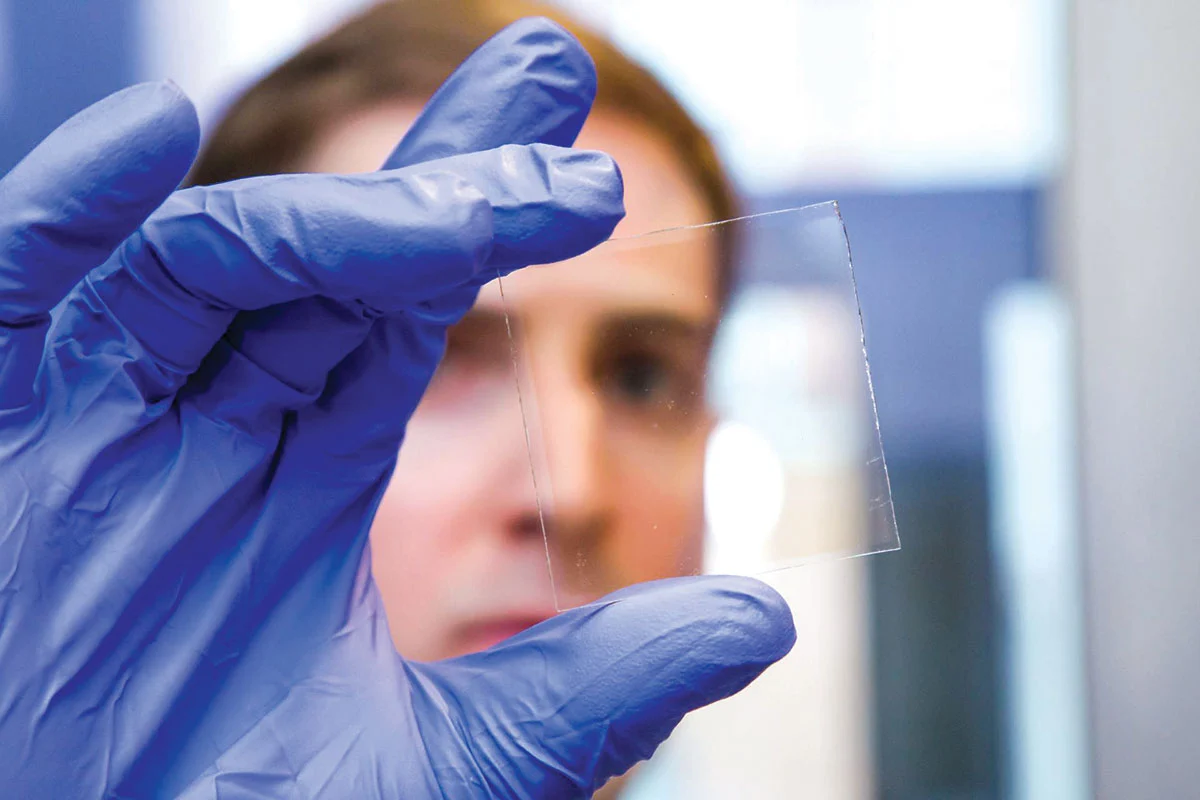
U prethodna dva izdanja časopisa PROZORI&VRATA ste mogli pročitati prvi i drugi deo ovog članka u kome smo predstavili hemijska svojstva stakla kao materijala, njegove karakteristike i mogućnosti primene u građevinskoj industriji. U drugom delu smo se bavili proizvodnjom stakla – postupcima od pečenja do oblikovanja. Sada sledi nastavak u kom ćemo Vam predstaviti postupke proizvodnje ravnog stakla, različite završne obrade i osnovne vrste stakla.
Proizvodnja ravnog stakla
Ravno staklo se do početka 20. veka proizvodilo duvanjem ili izvlačenjem širokog cilindra iz rastopa, njegovim rezanjem i izravnavanjem ili se iz lonaca lilo na čelične stolove i valjanjem pretvaralo u ravnu staklenu ploču. Danas postoji više postupaka mašinske proizvodnje ravnog stakla livenjem ili izvlačenjem direktno iz rastopa.
Fourcaultov postupak
Fourcaultov postupak nazvan je prema istoimenom belgijskom pronalazaču (1925. god). Staklene trake iz kadne peći izvlače se vertikalno kroz dugačku diznu od vatrostalnog materijala u obliku uskog razreza, koja pliva na rastopljenom staklu, slika 14.
Na početku rada dizna se utisne u rastop toliko duboko da kroz njen otvor prodire rastop koji prihvata ram spušten odozgo kroz mašinu. Izvlačenjem rama uvis počinje se oblikovati staklena traka. Ona prolazi kroz niz od 16-18 pari azbestom obloženih čeličnih valjaka, koji se nalaze u otvoru za hlađenje visokim 5-8 m. Neposredno nakon stvaranja traka se intenzivno hladi na oba ruba i tako dobija potrebnu mehaničku čvrstoću. Nakon napuštanja okna za hlađenje traka se automatski reže na željenu dužinu, a slobodno se režu ivice, jer su zadebljane. Fourcaultovim se postupkom mogu proizvesti staklene trake sa debljinom 1,5-7 mm. Brzina izvlačenja zavisi od viskoziteta stakla. Neposredno pre stvaranja trake viskozitet mora biti što veći, što zahteva nisku temperaturu izvlačenja. Kako ta temperatura zavisi od gornje temperature kristalizacije stakla, najviše se radi sa sastavima sa niskom temperaturom kristalizacije. Takvo je npr. staklo sastava 72,5% SiO2, 1,8% Al2O3, 4% CaO, 6% MgO i 15% Na2O3, sa temperaturom kristalizacije 890-960 °C. Hlađenje stakla na tako niske temperature ograničeno je u Fourcaultovom postpuku na dvostepenu površinu razreza dizne, kvalitet Fourcaultovog stakla zavisi od hemijske i termičke homogenosti stakla. Da bi se postigla što veća hemijska homogenost, potrebne su visoke temperature topljenja (1500-1550 °C).
Colburnov postupak
Colburnov postupak, zove se još i postupak Libbey-Owens, razlikuje se od Fourcaultovog po tome što se staklena traka izvlači sa slobodne površine istopljenog stakla, slika 15, dakle bez primene dizne za izvlačenje što je odlučujuće hlađenje ivica trake, a obavlja se hlađenje vodom.
Nedostatak ovog postupka je komplikovanost za izvlačenje, te potreba da se najmanje svakih 10 dana menja istrošeni valjak za promenu smera izvlačenja. Širina trake može iznositi 270-360 cm, debljine 1-30 mm.
Pitsburg postupak
Pitsburg postupak se karakteriše blokom od vatrostalnog materijala uronjenim nekoliko centimetara u stakleni rastop ispod mesta izvlačenja trake, slika 16.
Širina tog bloka je 30-80 cm, a zadatak mu je da staklo pri izvlačenju održava relativno hladnim i da stabilizuje strujanje rastopa. Početak izvlačenja trake pomažu vodom hlađeni valjci koji hlade ivice, a dalje se staklena traka vertikalno izvlači mašinom identičnom Fourcaltovoj mašini. Širina staklene trake može iznositi 220-320 cm.
Float postupak
Postupak float (prema engl. to float, plutati) razvila je 1959. godine firma Pilkington Brothers. Taj postupak premašuje sve ostale postupke proizvodnje ravnog stakla svojim kvalitetom i proizvodnim kapacitetom. Uređaji za pripemu sirovina omogućavaju izradu mešavine koja osigurava proizvodnju stakla izvanrednog konstantnog sastava. Prostor za odležavanje stakla u peći jednak je veličini prostora za topljenje, što omogućava dobro termičko homogenizovanje stakla. Rastop ohlađen na 1170 °C ističe iz kadne peći preko širokog izliva između para valjaka, slika 17 i rasprostire se po površini metalne kupke od rastopljenog kalaja.
Dubina metalne kupke je 30 cm. Širina 3-4 m, a dužina i do 50 m. Kupka se zagreva električnom strujom, i to tako da se u pojedinim delovima kupke mogu uspostaviti različite temperature. Te su temperature u području oblikovanja stakla takve da stvorene staklene trake za vreme svog hlađenja tokom 15-minutnog putovanja po površini istopljenog kalaja poprimaju izvanredna svojstva, vrlo ravnomernu debljinu i savršeno ravnu glatku površinu, dobijenu bez brušenja i poliranja. Pri temperaturi 1000-1030 °C, odnosno sa viskozitetom 103 Pa s, ravnotežna debljina staklenog rastopa na istopljenom kalaju 6 mm. Rastop se zatim hladi na 700 °C i stvrdne u traku koju prihvate valjci. Ako je potrebno da staklena traka bude manja, ona se ponovno zagrejava u jednoj od sekcija iste peći i razvlači se na željenu debljinu. Bitna je atmosfera iznad staklenog rastopa i metalne kupke. Ona mora biti neutralna ili slabo redukciona (azot sa 0,5 % vodonika) da bi se sprečila oksidacija kalaja i debljina sloja rastopa održavala ravnomernom, jer atmosfera iznad rastopa utiče na njegov površinski napon. Širina trake može iznositi 1,8-4,1 m, a mogu se izvlačiti debljine od 2-19 mm.
Valjanje stakla
Valjanje stakla se razvilo do livenja rastopa na ravnu površinu i izravnavanje valjkom. Kasnije se rastop iz lonaca izlivao među rotirajuće valjke. Danas je valjanje stakla, koje se naziva i livenjem, kontinuiran i automatski postupak za proizvodnju debelih staklenih ploča za ogledala i delove nameštaja, za ostakljivanje izloga i sl. Staklo se topi u kadnim pećima i preko posebnog izliva stalno lije među vodom hlađene valjke, koji ga oblikuju u kontinuiranu traku određene širine i debljine. Ako je površina stakla reljefna, dobija se ornamentno staklo. Umetanjem još jednog para valjaka za transport žičanog pletiva i deljenjem dotoka rastopa može se proizvoditi armirano staklo, slika 18. Oblikovana traka prolazi zatim kroz hladnjak.
Hlađenje stakla
Nakon oblikovanja jednim od postupaka prerade, staklo se hladi i prelazi iz žilavog i plastičnog u čvrsto stanje. Taj se prelaz događa u području transformacije između gornje i donje tačke hlađenja. Tom prilikom se staklo steže i postaje gušće, sve dok se ne uspostavi stabilno, ravnotežno stanje koje odgovara novoj, nižoj temperaturi. Hlađenjem stakla viskozitet postaje sve veći, a pokretljivost atoma sve manja, pa se povećava vreme potrebno za uspostavljanje stabilnog stanja. Ovo se može postići samo ako je hlađenje sporije. Ako se staklo brzo hladi, neće se skupljati ravnomerno. Zbog male toplotne provodljivosti stakla njegova se unutrašnjost neće tako brzo ohladiti, pa će se više skupljati i postati gušće. To će u staklu uzrokovati nehomogenost strukture i pojavu mehaničkih naprezanja. To su trajna naprezanja jer ostaju i nakon što se staklo potpuno ohladi i poprimi jednaku temperaturu u celoj masi. Kao posledica trajnih naprezanja pogoršavaju se mehaničke osobine stakla, odnosno smanjuje se kvalitet gotovih proizvoda, što se naročito odražava u njihovim optičkim osobinama, čvrstoći, gustini i sposobnosti zadržavanja stalnih dimenzija. Zbog toga se prilikom proizvodnje stakla nastoje trajna naprezanja što više smanjiti ili potpuno izbeći. To se postiže sporijim i kontrolisanim hlađenjem u području transformacije, i to neposredno nakon oblikovanja proizvoda, ili kasnije, naknadnim zagrevanjem već ohlađenog proizvoda i njegovim ponovnim, sporijim hlađenjem. Temperature hlađenja zavise od vrste stakla i debljine zida proizvoda. Za prozorska i ambalažna stakla one su između 540 °C i 550 °C, za olovna kristalna stakla 465-475 °C, za borosilikatna stakla 520-530 °C, a za bezalkalna stakla 660-680 °C.
Površinska obrada stakla
Većinu staklenih proizvoda za domaćinstva, čaše, zdele i ukrasne predmete od kristalnog i olovnog kristalnog stakla treba doraditi površinskom obradom, kojoj je cilj povećati kvalitet površine (površinsko brušenje, poliranje, duboko brušenje, graviranje, matiranje, nagrizanje i bojenje). Šuplji predmeti oblikovani duvanjem često imaju oštre ivice, koje nastaju otkidanjem ili rezanjem suvišnih delova. Ivice se izravnavaju brušenjem, a potpuno će se zaobliti i zagladiti topljenjem u plamenu. Ovo se naročito primenjuje u proizvodnji čaša. I velike staklene ploče za ogledala i izloge, dobijene livenjem i valjanjem, sa obe strane su hrapave i neravne, pa se moraju izravnati brušenjem i poliranjem.
Površinsko brušenje
Površinsko brušenje izvodi se brusnim sredstvom koje se pod pritiskom kreće po staklenoj površini. Kao brusno sredstvo najviše se upotrebljavaju korund ili elektrokorund, i to grublje granulacije za grubo brušenje, a finija za fino brušenje. Osim korunda, upotrebljavaju se i karbonind (silicijum-karbid) različitih granulacija.
Poliranje
Poliranjem se pripremaju vrlo fine i glatke površine. Mehaničko poliranje je slično brušenju, a upotrebljavaju se mekša sredstva, većinom fini prahovi na osnovu cerij-oksida. Površina stakla polira se i plamenom (plameno poliranje), a olovna kristalna stakla uranjanjem u kupatilo fluoridne i sulfatne kiseline određenog međusobnog odnosa i koncentracije (hemijsko poliranje).
Duboko brušenje
Duboko brušenje se primenjuje za ukrašavanje skupocenih staklenih predmeta. Brusi se rotirajućim brusnim pločama različitih veličina (prečnika 10-30 cm) napravljenim od korunda. Ornamentni ukrasi se prema šablonima urezuju automatizovanim mašinama. Staklene površine nastale brušenjem su hrapave i mutne, pa se naknadno ulepšavaju poliranjem.
Graviranje
Graviranje se od dubokog brušenja razlikuje po tome što su ukrasi plići i sitniji. Tako se na površini staklenih predmeta nanose fine linije, crteži i natpisi, koji se radi većeg kontrasta ostavljaju mutnim. Gravira se malim rotirajućim pločama koji su većinom od bakra, uz upotrebu nekog brusnog praha pomešanog sa prikladnim uljem. Vrlo fina gravura nastaje paranjem površine dijamantnim nožićem.
Matiranje
Matiranjem se površina stakla čini hrapavom, pa zbog toga postaje neprozirna. Pokrivanjem delova površine šablonima ili lakom mogu se postići različiti dekorativni efekti. Matirati se može hemijski (nagrizanjem) ili mehanički, ili injekcijom mlaza kvarcnog peska.
Nagrizanje
Dobro je poznato da je staklo prema delovanju fluornih spojeva, u prvom redu gasnog fluorovodonika, fluoridne kiseline i alkalnih fluorida, vrlo neotporno, da se lako površinski oštećuje ili čak otapa. Takvo delovanje zasniva se na hemijskoj reakciji fluora sa silicijumom i alkalnim elementima iz stakla. Prema sastavu stakla i prema upotrebljenom sredstvu za nagrizanje, dobijaju se na staklu različiti efekti: površinsko ili duboko nagrizanje, glatka i prozirna ili mutna, matirana površina. Pre nagrizanja moraju se delovi površine koji trebaju ostati nematirani, prekriti lakom ili lepljivom metalnom folijom. Razređena fluoridna (fluorovodonična) kiselina u smeši sa sulfatnom (sumpornom) kiselinom otapa staklo polako i jednolično, te ostavlja sjajne i vrlo glatke površine. Taj se postupak primenjuje za fino (hemijsko) poliranje stakla, a takođe i za njegovo ukrašavanje. Za tu se svrhu stakleni predmet prekrije voskom, prikladnim se alatom ili mašinom ucrtaju željeni ukrasi i oznake, te se predmet uroni u rastvor kiseline, pa će na mestima sa kojih je bio skinut zaštitni sloj ostati glatki udubljeni tragovi.
Površinsko bojenje stakla
Osim bojenja čitave mase stakla dodavanjem različitih oksida u sirovinsku smesu pre topljenja, površina staklenih predmeta se može dekorisati nanošenjem prikladnih sredstava za bojenje. Najčešće su to materije koje se sastoje od anorganskih pigmenata. Boja sa toplotnim istezanjem sličnim staklu meša se prvo sa terpentinskim uljem, nastala se pasta nanosi kistom ili pištoljem za raspršivanje. Nakon toga se stakleni predmet toplotno obrađuje pečenjem u tunelnoj peći.
Stakleni proizvodi
Svojstva stakla, budućih staklenih proizvoda mogu se već izborom različitih sirovina unapred odrediti, podesiti u širokom rasponu, pa je staklo tehnički materijal vrlo raznolike i svestrane primene. Zbog toga se u tvornicama stakla proizvode mnoge vrste stakla, odnosno raznovrsni stakleni proizvodi. Staklo za masovnu upotrebu svrstava se u ravno i u šuplje staklo, dok se u posebne vrste stakla ubrajaju ona sa specijalnim svojstvima i uskom specifičnom primenom kao što su laboratorijsko, optičko, građevinsko, elektrotehničko, sigurnosno, kvarcno, vodeno, penasto staklo, staklena vuna, staklena vlakna, staklo keramika.
Ravno staklo
Pod ravnim staklom se podrazumeva natrijusko-kalcijumsko staklo sa sledećim udelima pojedinih komponenata: 71-73% SiO2, 13-16% Na2O + K2O3, 9,5-13,5% CaO + MgO, 0,5-2% Al2O3. Takav sastav stakla određuje i njegova opšta svojstva, tabela 1. Svetlosna propustljivost zavisi od debljine stakla, ploča debljine 3 mm propušta 90-93% svetlosti, odnosno vidljivog spektralnog područja elektromagnetskog zračenja, dok se oko 3,5-4,5% svetlosti reflektuje. Toplotna otpornost takođe zavisi od debljine ploče te o razlici temperatura. Staklena ploča debljine 6 mm pući će pri temperaturnoj razlici od 100 K. Ravno staklo se prema nameni svrstava u više trgovačkih proizvoda. Najkvalitetnije staklo (kvalitet) služi za ostakljivanje nameštaja i polica.
Staklo za izloge
Staklo za izloge je natrijum-kalcijumsko-magnezijumsko staklo. Ravno staklo proizvodi se postupkom float, debljina mu je 5-8 mm i mora biti vrlo jednoliko. Savijeno staklo dobija se naknadnim zagrevanjem i savijanjem ravnih ploča.
Sigurnosno staklo
Sigurnosno staklo (trgovački nazivi: dupleks, tripleks) ugrađuje se kao zaštitno staklo u zaštitne naočale, gasne maske te prozore putničkih i drugih vozila. Takvo staklo je laminirano, tj. sastoji se od dve ili tri staklene ploče koje su slepljene sa međuslojem od savitljivog polimernog materijala. Ako sigurnosno staklo pukne, komadići ne odskaču i ostaju zalepljeni uz međusloj.
Armirano staklo
Armirano staklo je staklo pojačano žičanom mrežom, a obično se izrađuje u debljinama od 7-10 mm. Kao i laminirano, armirane staklene ploče su otporne na udare i ne rasprsnu se prilikom loma, pa se upotrebljavaju za ostakljivanje krovnih delova, za prozore i vrata radionica, fabričkih radnih prostorija, itd. U tabeli 1 su date osobine ravnog stakla.
Staklo za ogledala
Staklo za ogledala je ravno staklo proizvedeno postupkom float. Ogledalski sloj se najčešće sastoji od metalnog srebra koje se na površini stakla izlučuje iz rastopa (amonijačni rastop srebro-nitrata + rastvor nekog redukcionog sredstva) nakon hemijske reakcije sastojaka rastvora.
Ambalažno staklo
Ambalažno staklo obuhvata različite vrste boca za piće (boce za vino, pivo, žestoka pića, sokovi, bezalkoholna osvežavajuća pića, mineralna voda i sl.), staklenke za prehrambene proizvode, boce, spremnici za hemikalije, bočice za lekove, kozmetički proizvodi i sl. Ambalažno staklo se proizvodi u velikim količinama. Najčešće je to natrijumsko-kalcijumsko staklo, hemijski neutralno, prozirno ili obojeno, izrađuje se mašinski duvanjem. Staklo za bezbojne boce sadrži 71-73% SiO2, 12,5-13% Na2O, 9-12% CaO, 0,1-3% MgO i 1,4-2,5% Al2O3. Dodatkom oksida željeza, mangana ili hroma staklo se oboji zeleno ili smeđe. Cilindrični ili sferični oblik daje boci veću otpornost prema unutrašnjem pritisku. Površina boce može se od mehaničkih oštećenja dodatno zaštititi posebnim postupkom nanošenja tankog sloja metalnog oksida.
Borosilikatno staklo
Borosilikatno staklo sa dodatkom aluminijum-oksida naročito je otporno prema hemikalijama, a veoma otporno je prema temperaturnim promenama, pa se u hemijskoj tehnici upotrebljava za izradu laboratorijskog posuđa.
SiO2 staklo
SiO2 staklo se naziva i kvarcno staklo, a tehnički je veoma važno zbog svojih posebnih osobina, u prvom redu zbog izuzetnog malog toplotnog izduženja, velike toplotne otpornosti i propusnosti ultraljubičastog zračenja. Zbog visoke temperature topljenja, proizvodnja i prerada SiO2 staklo je skupo i složeno, ali se jednostavnijim postupkom i na nižim temperaturama može proizvesti staklo sličnih osobina. Za tu se svrhu smesa od 65-86% SiO2, 4-5% N2O i 10-30% B2O3 topi na 1550 °C, a zatim se toplotnom obradom na 600 °C staklo razdvaja u tri faze: natrijum-boratnu, bor-oksidnu i SiO2-fazu.
Kaljeno staklo
Kaljeno staklo je poznato i kao sigurnosno staklo, proizvodi se od običnog stakla posebnim toplotnim postupkom. Pri naglom hlađenju usijanog stakla površina mu se brzo skuplja, dok se meka unutrašnjost polako hladi, pa među slojevima nastaju velika naprezanja zbog kojih staklo postaje tvrdo i čvrsto. Takvo staklo podnosi veća mehanička i toplotna opterećenja od nekaljenog, ne može se rezati ni mehanički obrađivati, jer se i pri najmanjem površinskom oštećenju rasprsne u sitne komadiće.
Građevinsko staklo
Građevinsko staklo služi kao konstrukcioni građevinski materijal u obliku punih ili šupljikavih opeka, blokova i crepova. Po sastavu to je natrijumsko-kalcijumsko-silikatno staklo, a prednost stakla je kod građevinskog materijala, što je dekorativno, propušta svetlost, otporno je prema hemikalijama (industrijske prostorije) i prema učestalom delovanju vodene pare (kupaonice u bolnicama, zatvoreni bazeni i sl.).
Autori teksta: Prof. dr D. Škobalj, Ž. Đokić, dipl.ing.