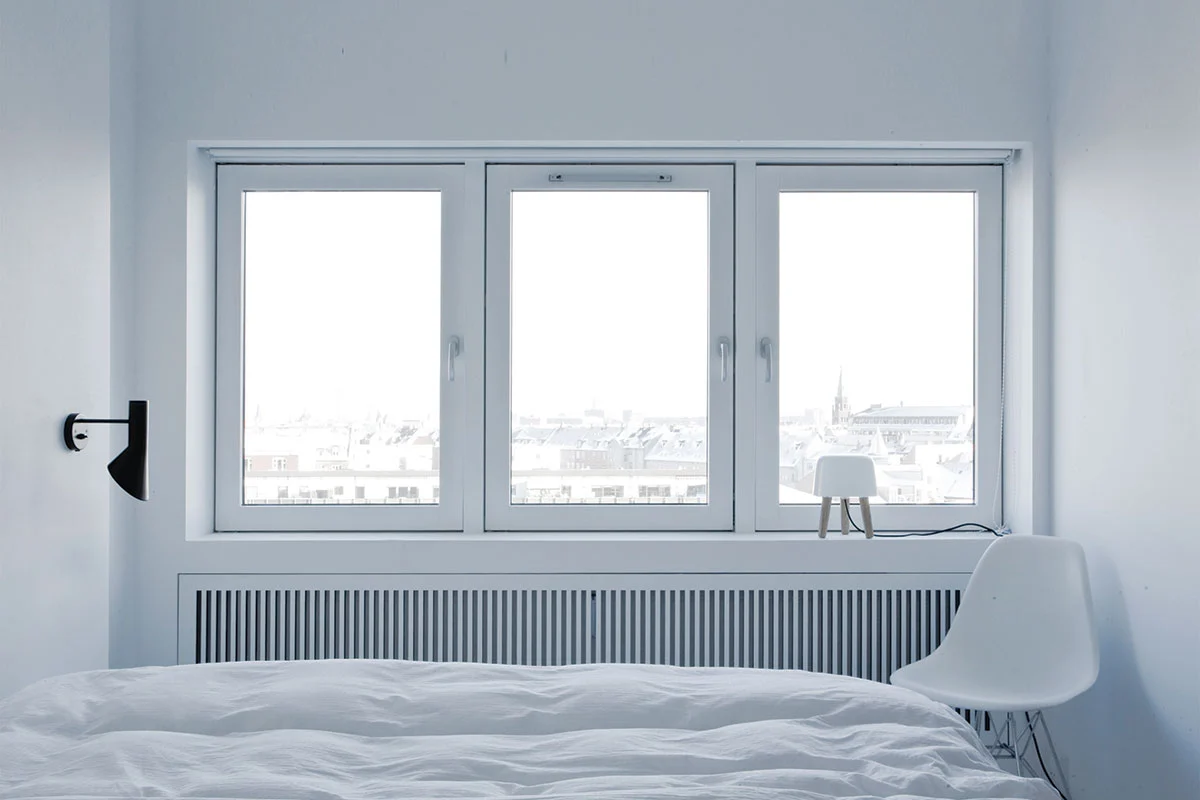
ISTORIJAT
Istorija PVC-a datira od prve sinteze vinil hlorida. Vinilhlorid je monomer koji je napravio Justus von Liebig 1835. godine. Prvi izveštaj o halogenom polimeru je objavio Hoffman 1860. godine, a prvi izveštaj o PVC-u je objavio Baumann 1872. godine. Fritz Klutte je otkrio osnove za tehničku proizvodnju PVC-a. Prva komercijalna proizvodnja PVC-a je započeta u USA dvadesetih godina prošlog veka.
Nemačka industrija je počela proizvodnju tridesetih godina prošlog veka, a proizvodnja u Velikoj Britaniji je počela četrdesetih godina. Od tog vremena postoji značajan razvoj u hemiji, koji je povezan sa stabilizacijom, u vezi toga sa radom na otpornosti na vremenske uticaje, što vodi do formulacija pogodnih za visoke tehničke primene u spoljnim upotrebama, poput prozorskih profila. Ovo je naročito dokazano u Nemačkoj gde se neplastifikovani PVC (PVC-U) koristi za proizvodnju prozora preko šezdeset godina.
PVC-U, GLAVNI ELEMENT I PROIZVODNJA
Osnovni element za proizvodnju PVC-U je PVC, koji se dobija polimerizacijom VCM. Osnova za proizvodnju VCM je morska so i nafta. Prvi korak je frakciona destilacija nafte i proizvodnja etilena.
Drugi korak je razlaganje kuhinjske soli na NaOH (natrijum hidroksid) i hlor (Cl).Treći korak je reakcija etilena, hlora i proizvodnja etilen dihlorida. Četvrti korak je krekovanje etilen dihlorida, proizvodnja VCM. Polimerizacijom VCM se dobija PVC. Na slici 1 je data šema proizvodnje PVC praha.
PVC PRAH
VCM se proizvodi kao tečnost pod pritiskom u polimerizacionom postrojenju. VCM može biti polimerizovan – masena polimerizacija, alternativno može biti proizveden pomoću suspenzionog ili emulzionog procesa.Suspenzioni proces se najviše koristi u Engleskoj. Ovaj proces uključuje mešanje VCM sa odgovarajućom količinom vode pre polimerizacije, i proizvodi se polimer sa relativno krupnozrnastim česticama (prečnika oko 0,1 mm). Suština je dobiti polimer specifične dužine lanca, uske oblasti viskoziteta i fizičkih osobina. Za različite primene se koriste materijali različitog viskoziteta. Za tipične prozorske profile reakcija praha će se odigrati na oko 57°C. Ovim se dobija odgovarajući viskozitet, sa gustinom od 580 kg/m3 i poroznost između 21 i 23%. Na slici 2 je prikazana hemijska struktura PVC-a.
Jedan od elemenata za proizvodnju PVC je hlor. Hlor je značajno veći element u poređenju sa ugljenikom ili vodonikom. Za ekstruziju prozorskih profila od PVC-U koriste se dva glavna bazna polimera. Oba su proizvedena suspenzionim procesom.
Jedno je homopolimer aproksimativnog K65 do K68 viskoziteta. Drugi je akrilni kopolimer, tipično sadrži 8% akrila. K vrednost je mera molarne mase, broj monomera vinil hlorida u PVC makromolekula. K vrednost takođe daje meru viskoziteta polimera, što je viša K vrednost viši je viskozitet polimera. Sistem kopolimera vodi ka poboljšavanju fizičkih osobina, što je uzrokovano lancima akrilnog kopolimera koji obezbeđuje dobru akrilnu disperziju (akril deluje kao udarni modifikator).
Najveći deo tržišta EU koristi homopolimer, uglavnom zbog niže cene, ali i veće dostupnosti. Kada biramo stepen homopolimera treba obratiti pažnju da viša K vrednost (tj. viša molekularna težina) daje bolje fizičke osobine, ali pravi veće poteškoće u procesu prerade. Kod ekstruzije prozorskih profila viskozitet je praktično diktiran zahtevima procesa i toka.
UDARNI MODIFIKATOR
Ako se koristi homopolimer zahteva se udarni modifikator tako da popravi fizičke osobine. Funkcija udarnog modifikatora je primarno da spreči propagaciju pukotine koja se može manifestovati većom deformabilnošću. Da bi se ovo izbeglo mora da postoji dobra disperzija modifikatora. Na ovo delotvorno utiču male čestice gume u PVC matrici. Funkcija ovih gumenih čestica je da se spreči progresivno pucanje kroz profil.
Postoji široki opseg tipova udarnih modifikatora koji su pogodni za korišćenje sa tvrdim PVC-om. Samo su dva podesna kao proizvod, koji se koristi za vanjsku upotrebu. Dva tipa koji su otporni na atmosferske uticaje su: akrilna jezgra i hlorovani polietilen (CPE). Najviše je u praksi korišćeno jezgro od akrilonitrilne gume sa poli-metil-metakrilitalnom prevlakom. Trenutno se koriste tri vrste akrilnih modifikatora. Najveću udarnu žilavost pokazuje PVC-U koji koristi udarni akrilni modifikator FM 50. Iznad adekvatne temperature prerade kod njega dolazi do bržeg pada udarne žilavosti. Na slici 3 je data udarna žilavost od različitih vrsta udarnih modifikatora (FM 20, FM 22).
Na slici 4 je data zavisnost ugaone čvrstoće vara od temperature za pojedine vrste modifikatora (FM 22, FM 50).
PROCESNO SREDSTVO
Procesno sredstvo se dodaje zbog dva razloga. Prvi razlog je osiguravanje čvrstoće topljevine, koja je izuzetno važna za početak rada ekstruzione linije. Drugi razlog je obezbeđivanje stabilne proizvodnje.
Startovanje ekstruzione linije uključuje provlačenje topljevine polimera kroz seriju kalibrisanih alata (radi ostvarenja dimenzija), kao i jedinice za izvlačenje. Za vreme procesa kalibrisanja topljevina je izložena mlazu vode, koji vrši hlađenje. Za odstranjivanje gasova se koristi vakuum, a vučna sila obezbeđuje kretanje profila kroz kalibrator. Procesno sredstvo ima zadatak kontrole vremena fuzije, potrebno je obezbediti da se prahovi spajaju u oblik neprekidne mase.
Izuzetno je važno obezbediti dovoljno želiranja u vakuumskom delu ekstrudera, koji je približno na pola puta vijka. Na taj način je ostvareno da se pomoću vakuuma uklone svi ostaci isparljivih materija, zarobljena vlaga, a nema ni usisavanja praha.
Zarobljena vlaga dolazi iz skladišta sirovog materijala, npr. punioca, koji je veoma higroskopan. Postoji tačka gde je kompaund preželiran, što rezultuje da je “previše” prerađen materijal, što uzrokuje oštećenje molekula cepanjem lanca u završnoj fazi vijka. Ovo je veoma važno za fizičke osobine. Preveliko želiranje,takođe dovodi do niže vrednosti otpornosti na starenje, što uzrokuje veću potrošnju elemenata za stabilizovanje.
Najpopularnija procesna sredstva za koršćenje su: kopolimeri metil-metakrilata, stiren/akrilne mešavine, monopolimer metakrilat-PVC i alfa metil stiren.
Zbog velike molekularne težine, mešavina procesnog sredstva ojačava kraće PVC lance koji se efektivno vezuju s njima u više elastičnu masu (topljevinu). Ispitivanja pokazuju da porast koncentracije procesnog sredstva promoviše bržu fuziju (želiranje), ali uzrokuje i porast osobina nepovratnosti dimenzija usled delovanje toplote.
PUNIOC
Glavna funkcija dodavanja punioca je da se smanji cena. Oni osiguravaju da neorganska masa pomaže unapređenju mehaničkog rada ekstrudera.Najuobičajeniji punioc koji se koristi u prozorskim formulacijama je stearinska kiselina, koja prevlači kalcijum karbonat.
Ovaj materijal se prirodno pojavljuje i odgovoran je za mlevenje čestica manjih dimenzija.
Da bi se ostvarila konkurentna cena prozora, svi proizvođači koriste punioce primarno prevučene stearatom, a ne istaložene punioce. Iakoistaloženi punioci imaju manje čestice i aktiviraju fizičke osobine, oni su sada značajno skuplji nego prevučeni punioci i cena im je slična ceni PVC praha.
Prevlaka stearata se dodaje da pomogne prilikom prerade. Obloga (prevlaka) pomaže vezivanju punioca i materijala i na taj način se obezbeđuje rano želiranje.
Druga važna osobina je da deluje kao podmazivač koji sprečava površinsku koroziju neorganskih blokova.U tabeli 1 su dati tehnički zahtevi i tipične osobine punioca.
PIGMENTI
Kao beli pigment se koristi rutilni titan dioksid. Glavni razlog za dodavanje titan dioksida je da osigura belu boju. To je važan element kompaurida koji treba da osigura neorgansku masu kompaurida. Titan dioksid je relativno skup u poređenju sa PVC–om. Postoje različiti tipovi titan dioksida. Neke klase proizvode efekat poznat kao iscvetavanje. Ovo je pojava kada za vreme životnog ciklusa proizvoda određena količina titan dioksida migrira ka površini proizvodeći efekat belenja.
Visoki stepen iscvetavanja je uobičajen kada se koristi kalajni stabilizator. Kompletan opseg tonera boje može biti dodat kompaundu. Veliki broj kompanija ima sopstvenu nijansu bele boje. Toneri boje se dodaju u veoma malim količinama, a obično je potrebno više od jednog.Toneri su obično plavi, moderni potrošači više vole plavkasto belu boju.
STABILIZATOR/LUBRIKANT
Stabilizator/lubrikant može biti dodavan kao jedan sastojak ili kao „one pack system”. Korišćenje sistema „one pack“ omogućava pristup proizvođača prozora savremenim tehnologijama. Za moderne jedinice za proizvodnju suve mešavine „one pack“ je mnogo lakše koristiti u procesu proizvodnje. Suština je da se dodaje jedan kompaund i tačnost merenja je manje važna nego kada se dodaje više osebnih elemenata, sa potrebom veće tačnosti i skupljim sistemom merenja.„One pack“ sistem se sastoji od primarnog stabilizatora, ko-stabilizatora i lubrikanta i ponekad tonera. Ovo je najkomplikovaniji i uobičajeno kritični aditiv.
Zbog komercijalne osetljivosti nijedan isporučilac neće dati tačan sadržaj „one pack“, i samo se daju detaljne osnove stabilizatora, npr. barium (kadmijum) olovo sa njihovim odnosom, potpuno olovni ili kalcijum/cink.
Stabilizatori koji za osnovu imaju barijum i kadmij su zabranjeni u upotrebi, jer su dokazano kancerogeni. Naknadno je dokazano i da je to i olovo, u zemljama EU je zabranjeno njegovo korišćenje nakon 2015. godine. Stabilizator koji za osnovu ima olovo još se koristi u Indiji i Kini. Sve veći broj proizvođača PVC-U za stabilizator koristi onaj koji za osnovu ima Ca/Zn.
Poznato je da je glavna spoljašnja manifestacija toplotne degradacije PVC-a razvoj hlorovodonika, razvoj boje i pogoršanje fizičkih, hemijskih i električnih osobina. Dehidrohlorovanje uključuje progresivno kretanje atoma vodonika, hlora duž lanca polimera. Stabilizator mora da da i toplotnu i UV stabilnost. Toplotna stabilizacija se uglavnom zahteva zbog prerade, ali takođe i za zaštitu u toku upotrebe. UV stabilizacija se zahteva da bi se proizvodu obezbedio određeni životni vek. Ovi stabilizatori moraju biti dodati dovoljno, tako se posle prerade obezbedi odgovarajuća zaštita, koja će ekstrudiranom profilu obezbediti odgovarajući životni vek.Utvrđeno je da će stabilizator reagovati predominatno sa slobodnom HCl.
Šematski dijagram delovanja stabilizatora je prikazan na slici 5. Slika pokazuje da je PVC predmet grejanja, smicanja i UV za vreme prerade ili upotrebe. Ove procese uzrokuju dehidrohlorovanje i razvoj HCl molekula. Funkcija stabilizatora je da počisti ove HCl molekule i spreči od daljeg delovanja koje dovodi do kidanja lanaca.
Tradicionalni stabilizatori takvi kao što su barijum/kadmijum/olovo i svi stabilizatori koji za osnovu imaju olovo su relativno jednostavni. Sadrže samo sve komponente i za optički izbistrivač se koristi fostat. Ovaj stabilizator se koristi samo u Aziji (Kina, Indija).
Noviji sistemi zasnovani na kalcijum/cink (Ca/Zn) su mnogo komplikovaniji i zahtevaju odgovarajući raspored kostabilizatora, što osigurava održavanje boje, UV stabilnost, optičku bistrinu i pojačanu toplotnu stabilnost.
OLOVO KAO STABILIZATOR
Metalne soli i sapuni
Neke prednosti i mane stabilizatora su:
- osigurana otpornost na starenje
- visoka specifična masa
- teški metal-toksičan
- jeftiniji od sistema koji sadrži kadmij
- manje tolerantnija prerada nego kada se koristi sistem koji sadrži kadmij
KALAJ KAO STABILIZATOR
Organski kompaund
- neki oblici imaju manju toksičnost
- neugodan miris
- bitno vezivanje
- relativno mala specifična masa
- relativno skup
- podnose unakrsno bojenje
- zahteva visoki nivo titan dioksida i materijal postaje veoma abrazivan
Ca/Zn STABLIZATOR
Metalni sapuni i organski kompleks
- ljudski oligoelementi
- bitno samopodmazivanje
- neefikasan stbilizator, zahteva kostabilizatore
- relativno skup
- nije sasvim siguran
- manja tolerancija prerade
PODMAZIVAČI
Lubrikanti su izuzetno važni prilikom prerade PVC-a, uprkos činjenici da se oni koriste sa veoma malim nivoom dodavanja. Lubrikanti se dodaju obično između 0,5 i 1,0 phr. Lubrikanti sprečavaju lepljenje materijala sa metalnim površinama mašina za preradu i takođe pomažu regulaciju brzine želiranja kompaunda unutar opreme za preradu.
Različiti lubrikanti imaju različit efekat na ponašanje želiranja, pošto oni ne samo što deluju između PVC čestica nego i metalne površine. Neki lubrikanti se delimično apsorbuju u PVC zrnu i efektivno proizvode „rebra“ na česticama, uzrokujući porast trenja između zrna i tako promovišu raniju fuziju.
Ovi lubrikanti su klasifikovani kao delimično kompatibilni. Drugi lubrikanti su nekompatibilni i ne mogu biti apsorbovani u PVC. Ovi efektivno podmazuju između čestica smanjujući trenje i usporavajući brzinu fuzije.
Izbor lubrikanata je kompleksan i može se koristiti za veliki broj različitih proizvoda.Izbor lubrikanata je zavisan od drugih aditiva unutar sistema. Neki aditivi mogu delimično apsorbovati neke podmazivače. Naročitu pažnju treba obratiti kada se bira kombinacija lubrikanata kao i njihov relativni udeo, uvreženo je mišljenje da pojedini lubrikanti reaguju jedni na druge.
Nekorektna kombinacija ili prekomerni nivo koji su utvrđeni kod laboratorijskih ispitivanja mogu uzrokovati probleme prilikom korišćenja. Problemi se manifestuju kao gradnja zaostalog voska u dizni koji uzrokuje dekompoziciju. Izbor sistema lubrikanata koji se koristi utiče na efekat reologije mase.
Izbor lubrikanta koji se koristi kao i njegov nivo zavisi od ekstrudera i alata. Korektna ravnoterža lubrikanata obezbeđuje uniforman tok kroz alat kao i punjenje dizni. Ravnoteža lubrikanata ima veoma značajan efekat na želiranje kompaunda i ostvareni stepen prerade.
PRERADA KOMPAUNDA
Prerada kompaunda se izvodi u dva koraka:
- prvi korak je priprema prozorskog kompaunda koji se često naziva suvi prah,
- drugi je ekstruzija kompaunda u profil.
PROIZVODNJA SUVOG PRAHA
Proizvodnja suvog praha se odigrava u mešaču velike brzine. Na slici 6 je data tipična organizacija mešača. Svi sirovi materijali se dodaju u komoru mešača u jednom koraku. U nekim situacijama se punioc i pigment dodaju za vreme mešanja, kada početno punjenje dostigne temperaturu od 90°C. Ovim kasnijim dodavanjem se smanjuje habanje miksera i veruje se da daje jasniju boju.
U komori mešača postoje lopatice koje rotiraju velikom brzinom u oblasti 2500 o/min, uzrokujući da se materijal greje indukovanim trenjem. Za vreme procesa grejanja materijal teče unutar komore. Ako je korišćeno korektno odmeravanje i setovanje praha u komori se formira vrtlog. Vrtlog obezbeđuje da se sav sirovi materijal meša zajedno. Ovo je potmognuto podmazivanjem mase i apsorpcijom u polimernu matricu. Grejanjem PVC zrna se otvaraju i delimično apsorbuju podmazivače.
Neki lanci lubrikanata se umeću u PVC zrna efektivno formirajući rebra, koja štrče od individualnih zrna. Ova delimična apsorpcija omogućava dobru disperziju podmazivača kroz mešavinu. Podmazivanje mase je u oblasti temperatura od 60°C do 100°C. Materijal se meša između 110°C i 120°C, na toj temperaturi masa postaje kao pasta.
Topla mešavina se tada prebacuje u komoru, koja ima oblast za hlađenje materijala. Materijal se dalje meša mnogo manjom brzinom, dok mešavina ne bude ohlađena do ispod 40°C. Za vreme ovog procesa PVC zrna se zatvaraju spajanjem sa lubrikantima. Na ovoj temperaturi svi lubrikanti će ponovo očvrsnuti. Ovaj materijal tada normalno prolazi kroz sito pre skladištenja i distribucije.
Neki materijali se tope i velikom silom vrše pritisak na zidove komore i dolazi do lepljenja izvesne količine materijala na zidove toplog mešača. Materijal koji se lepi na zidove komore uglavnom je neorganski materijal koji se veže sa lubrikantima i zato je veoma tvrd. Periodično, nešto ovog materijala poznato kao škriljac se lomi dalje od mešača. Veoma je važno prosejavanje ovih čestica, kao i da ne dođu do ekstrudera i pojave se na površini ekstruderanog profila, kao tačkasta korozija.
EKSTRUZIJA PROFILA
Ovo je proces pretvaranja suvog praha u neprekidni termoplastični materijal. Ovaj proces se izvodi koristeći ekstruder sa dva vijka, koji se obrću u suprotnim smerovima. Ekstruder je jednostavnog oblika, ovalno oblikovani barel (cilindar) u koji su instalirana dva puzna vijka i spoljnjeg trakastog grejača oko barela.
Postoje generalno dva tipa ekstrudera koji se koriste za proizvodnju prozorskih profila. Oni su klasirani kao konični i paralelni. Ova imena se odnose na geometriju vijka. Dimenzije i kapacitet ekstrudera su funkcija prečnika vijka i njegovog odnosa sa dužinom.
Paralelne mašine koriste vijke u oblasti prečnika od 65 mm do 110 mm, konične mašine u oblasti od 35 do 80 mm. Konični ekstruder koji ima vijak sa prečnikom vrška od 58 mm, ima sličan kapacitet kao i paralelni ekstruder sa prečnikom vijka od 90 mm. Dužina vijka ima glavni uticaj na provedeno vreme. To je vreme koje suvi prah (dry blend) provode u barelu (cilindru).
Novije mašine koriste veći odnos L/D (L-dužina vijka, D-prečnik vijka). Ovo dozvoljava da se materijal prerađuje laganije ili porastom brzine vijka kapacitet postaje viši. Vijci imaju dve osnovne funkcije:
- prva funkcija je transport suvog praha od levka do alata i guranje viskozne mase kroz alat za oblikovanje,
- druga funkcija je osiguranje smicanja, koje će pomoći masi suvog praha da pređe u viskoznu homogenu masu.
Ova viskozna masa se prisilno provodi kroz alate koji daju zahtevani oblik profila. Masa se tada hladi izvlačenjem kroz seriju kalibrisanih alata. Ovi alati se hlade vodom i poseduju vakumske otvore radi izvlačenja mase na metalnimm površinama. To je korak kada se masa hladi i očvršćava u korektan oblik, površina je polirana da bi se postigla glatkoća.Za vreme procesa ekstruzije vijak prenosi rad na materijal, tako da se menja struktura matrice želiranjem i izvodi se želiranje sastavnih delova zajedno. Postoje različiti sastavni elementi, npr. udarni modifikator, koji se ne želira u matrici, ali mora biti mešan kroz masu da obezbedi jednaku disperziju kroz završni proizvod. Ova disperzja i stepen rada imaju začajan efekat za određivanje osobina konačnog profila.Postoje četiri posebne zone duž vijka.
Prva zona je zona kompresije. Funkcija ovog dela je da se materijal sabije zajedno i dobije dobra disperzija oko zavojnog vijka. Materijal progresivno ide duž ove sekcije i počinje vezivanje između sebe, kao i topljenje materijala. Druga zona je zona devolatizacije. Primarna funkcija ove zone je da ukloni zarobljene gsove, poput vlage. Treća zona je druga kompresiona oblast. Ova oblast je odgovorna za konačno topljenje materijala i obezbeđuje želaste mase. Četvrta zona je zona merenja. Karakteristika ove zone je da se u njoj materijal meša u potpuno homogenu mešavinu i na taj način se omogućava isporuka materijala pri konstantnim uslovima.
Najjednostavniji proces želiranja sadrži nekoliko koraka. Početni korak je disperzija aditiva i početak prekida ili početak topljenja zrna. Kako se toplota i smicanje primenjuju, ovo topljenje se nastavlja. Na slici 7 je dat šematski prikaz procesa ekstruzije.
Postoji više promenljivih parametara u procesu ekstruzije koji moraju biti kontrolisani. To omogućava radnicima u proizvodnji odgovarajuću količinu rada u materijalu i da na takav način obezbedi kvalitetne osobine profila. Glavne varijable koje se kontrolišu su:
- Temperatura barela (cilindra). Zone barela ekstrudera su grejane spoljnim trakastim grejačem i u kasnijim zonama hlađeni ili vazdušnim duvaljkama ili cevnim zmijama kroz koje struji voda. Podešavanje temperature zona cilindra omogućava kontrolu prekomerne fuzije i toka materijala.
- Tempretura vijka. Ovo je omogućeno na nekim ekstruderima i pomaže kontroli fuzije i toka materijala. Porast temperature vijka će pomoći promociju rane fuzije i teži promociji toka ka centru.
- Temperatura alata. Kontrola temperature pomaže balansiranju toka kao i obezbeđenje sekundarnih karakteristika, koje mogu uticati na površinski sjaj i boju. Sa istrošenim alatom tok može biti korigovan, do izvesnog stepena setovanjem nejednakih temperatura oko alata.
- Brzina doziranja. Brzina doziranja kontorliše popunjenost zavojnica vijka. Ako su zavojnice pune onda će vijci prerađivati tvrdi materijal putem energije smicanja.
- Brzina vijka. Brzina vijka je drugi način kontrolisanja količine rada smicanja koji ide u materijal. Ako se vijak drži pun, brzina vijka kontroliše kapacitet ekstrudera.
- Brzina linije. Ovo je veličina koja karakteriše brzinu kojom se polimerni materijal vuče od alata. Brzina linije se koristi za kontrolu debljine zida profila.
- Vakuum. Vakuum uklanja sve zarobljene gasove iz mase. Ako se gasovi ne odvedu, tada će površina profila biti siromašna.
- Temperatura vode za hlađenje. Sa količinom protoka vode kontroliše brzinu hlađenja polimernog materijal i količinu zaostalih napona u profilu.
U tabeli 2 su date varijable koje utiču na karakteristike profila.
PVC-U prozori imaju više osobina koje ih čine jedinstvenim. Ključne osobine su:
OTPORNOST NA STARENJE
U zadnjih trideset pet godina provode se ekstenzivna istraživanja vezana za otpornost na starenje u laboratoriji i u praksi. To je deo standarda EN513. Ovim standardom se definiše ne samo otpornost na sunčevog zračenja nego i zadržavanje udarne čvrstoće. Ispitivanja su provođena izlaganju radijacije od 8 GJ/m² koja je ekvivalentna desetogodišnjem izlaganju u severnoj Evropi.
KRUTOST PROFILA
Krutost profila je ispitivana u cilju utvrđivanja modula elastičnosti kod istezanja i savijanja, EN ISO 178 (Determination of flexural properties – Određivanje elastičnih osobina). Rezultati ispitivanja pokazuju da najveći broj profila ima modul elastičnosti veći od preporučene minimalne vrednosti specificirane u standardu.
UDARNA ČVRSTOĆA
Utvrđivanje udarne čvrstoće se izvodi na nekoliko načina. Jedan od načina je test udara. Profil se drži u zamrzivaču 1 sat na temperaturi – 10°C i izlaže se padanju polukugle mase 1 kg sa visine 1 m u skladu sa EN 12608-1 Unplasticized poly (vinyl chloride) (PVC-U) profiles for the fabrication of windows and doors – Classification, requirements and test methods – Part 1: Non-coated PVC-U profiles with light coloured surfaces. Drugi test je test udarne žilavosti i poznat kao Šarpijev test.
TOPLOTNA OTPORNOST
Otpornost materijala prema deformaciji pod opterećenjem se utvrđuje Vikatovom temperaturom omekšavanja. Tipično ostvarene vrednosti su oko 80°C.
DIMENZIONA STABILNOST
Utvrđivana je dimenzionatna stabilnost profila grejanjem do 100°C. Maksimalno dozvoljeno skupljanje od 2% je lako ostvareno.
IZOLACIONE OSOBINE
PVC-U ima nisku toplotnu provodljivost, praktično je prenos toplote kroz materijal mali, efektivno eliminisana je bila kakva kondenzacija na profilu.
OTPORNOST PREMA HEMIJSKOM UTICAJU
PVC-U se karakteriše visokom otpornošću prema hemijskom uticaju i zaprljanju okoline, takođe je otporan na brojne hemikalije.
Pišu: Prof. dr Dragan Škobalj, Žarko Đokić, dipl. inž.